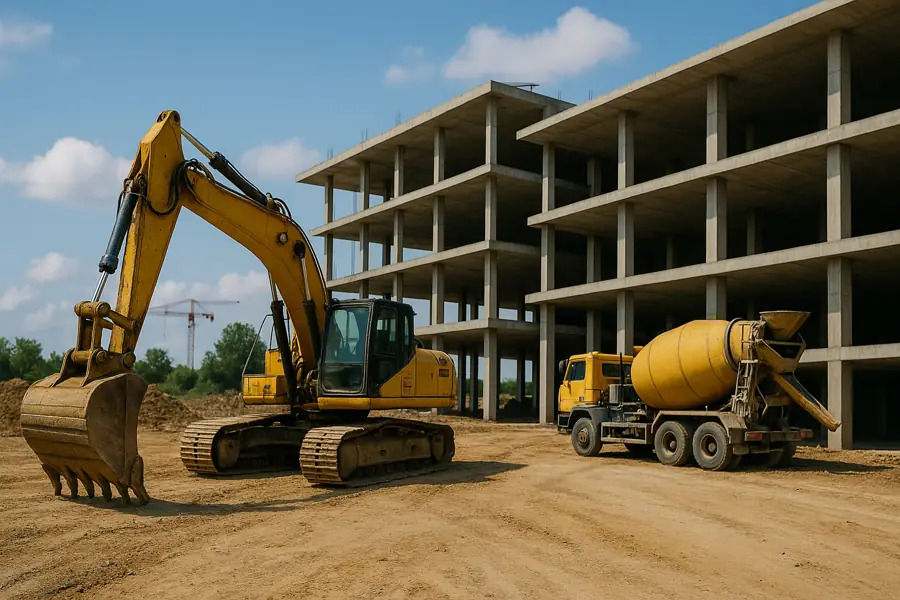
Estimate vs Reality: How to Accurately Calculate the True Unit Cost of Each Task on Your Construction Sites
🏗️ Introduction
In the construction industry, many companies know how much they invoice… but very few know how much each task actually costs them once executed on site.
Often, during the bid preparation, unit prices are based on production rates, standard resources, or sometimes just reused from past estimates. Once the works are completed, they simply check the overall margin—without analyzing the cost of each line item.
Yet, this information is crucial to:
-
Avoid recurring estimation mistakes
-
Identify unprofitable tasks
-
Adjust future prices more accurately
-
Improve overall project management
This article offers a practical, step-by-step guide to calculating the true unit cost of each task in your construction projects—using your existing tools or a dedicated software like PROTRACKBTP.
🎯 Why Calculate Unit Costs Task by Task?
🔍 1. To Refine Your Future Estimates
By comparing forecasted prices to actual expenses, you enhance the accuracy of your bids. No more guesswork—just data-backed decisions.
💸 2. To Protect Your Margins
A project might seem profitable overall, yet some line items can be heavily in the red. Without detailed monitoring, these losses remain invisible.
📚 3. To Build an Internal Cost Database
Recording your actual costs helps you build a tailored pricing reference that reflects your methods, teams, and field conditions.
🏛️ 4. To Better Advise Project Owners
Public and private clients can also benefit from this approach to more realistically evaluate their project budgets.
🧮 What Is Meant by Actual Unit Cost?
It refers to measuring how much a specific task (or “unit price number”) actually cost you once executed on site.
What it includes:
-
Labor (hours worked × hourly rate)
-
Materials actually used (quantity × unit price)
-
Equipment (usage time × hourly cost)
-
Additional costs (energy, transport, disposal, etc.)
📌 Simplified Example
Line item: 01.02 – Concrete slab demolition
Client unit price: €58.5/m²
Markup coefficient: 1.3
Estimated unit cost: €45/m²
Executed quantity: 100 m²
Invoiced amount: €5,850
Real cost :
Resource | Quantity | Unit Cost | Total |
---|---|---|---|
Labor | 80 h | €45 | €3,600 |
Dump truck | 8 h | €100 | €800 |
Loader | 8 h | €100 | €800 |
Disposal fees | – | – | €50 |
Total | €5,250 |
➡️ Actual unit cost: €5,250 / 100 m² = €52.50/m²
➡️ Compared to the estimated cost of €45/m², this task generated a lower-than-expected margin.
🛠️ How to Calculate Actual Costs per Task?
1. Use Your Daily Site Log
The site log tracks on a daily basis:
-
Present workers
-
Equipment used
-
Delivered and consumed materials
-
Activities carried out
👉 Simply add multiple columns such as 'Activity No. / Quantity' to break down the resources consumed across the appropriate tasks. This way, it will be possible to determine the share of each resource consumption allocated to each activity.
2. Use an Excel Spreadsheet
A good table will help you:
-
Assign each resource to a task
-
Multiply by its unit cost
-
Add up actual costs per line item
-
Compare with invoiced amounts
📌 Example columns:
-
Date
-
Activity
-
Unit Price Number
-
Worker / Equipment / Material
-
Quantity used
-
Unit cost
-
Total spent
3. Automate Tracking with PROTRACKBTP
PROTRACKBTP simplifies everything:
-
Allocation of consumption to each line item
-
Automatic tracking of executed quantities
-
Real-time cost calculation
-
Detailed reports per resource used
-
User-friendly and collaborative
🎯 Ideal for construction companies that want to scale up without complicating their processes.
📊 Make the Most of Your Data
Tracking actual costs per line item isn’t just a technical step—it’s a strategic tool. Use it to:
-
Spot consistently over-budget tasks
-
Understand your execution bottlenecks
-
Rework your pricing catalog
-
Negotiate smarter with project owners
📘 Case Study – Done with PROTRACKBTP
🏗️ Project Overview
- Type: Foundation for an office building
- Task analyzed:
03.01.004 – Continuous footing in reinforced concrete (350 kg/m³ dosage)
- Sale price: €425/m³
- Markup coefficient: 1.25
- ➡️ Estimated raw cost = €425 / 1.25 = €340/m³
- Executed quantity: 30 m³
- Amount invoiced: €12,300
📊 Budget Forecast (as per cost study)
🔨 Labor
Role | Hourly Rate | Estimated Hours | Total |
---|---|---|---|
Mason | €23 | 40 h | €920 |
Formworker | €22 | 32 h | €704 |
Rebar Worker | €22 | 16 h | €352 |
Laborer | €18 | 32 h | €576 |
Total | €2,552 |
🚧 Equipment
Equipment | Hourly Rate | Hours | Total |
---|---|---|---|
300L Concrete Mixer | €15 | 10 h | €150 |
Vibrating Poker | €10 | 6 h | €60 |
Total | €210 |
🧱 Materials
Material | Quantity | Unit Price | Total |
---|---|---|---|
Cement (50 kg) | 231 bags | €8.5 | €1,963.5 |
River Sand | 18 m³ | €38 | €684 |
Gravel 5/15 | 21 m³ | €44 | €924 |
Water | 12 m³ | €2 | €24 |
Steel | 2400 kg | €1.6/kg | €3,840 |
Total | €7,435.5 |
At 50% progress (15 m³ completed), here’s what PROTRACKBTP showed:
➡️ Observed cost per m³: €405
➡️ Which exceeds the estimated cost of €340
A closer look at material consumption:
-
Materials already cost €4,651, which is over 62% of the planned material budget (€7,435.5), while only 50% of the work is done.
-
Cement: €1,275 already spent → 65% of budget
-
Steel: 66% of budget already used
Possible Reasons:
-
Incorrect material quantity estimation
-
Poor resource management on site
➡️ Tracking in real-time allows the company to take corrective action early.
Without it, the overrun might only appear at the end of the project—possibly unnoticed if the overall project remains profitable.
✅ Best Practices for Effective Monitoring
-
Start small: Track 3 to 5 key tasks on a pilot project
-
Involve your team: Site managers and foremen must understand the value of tracking
-
Standardize tools: Use the same daily log template and Excel table
-
Analyze regularly: Weekly or by project phase
-
Summarize at the end: Final report comparing forecast vs actual per line item
🏁 Conclusion
Tracking unit costs per task is no longer a luxury reserved for large contractors. It’s a powerful, accessible lever for SMEs and consultants to:
-
Secure their margins
-
Fine-tune their offers
-
Make data-driven decisions
With simple tools—or a solution like PROTRACKBTP—this becomes a modern management reflex that brings measurable value.
📢 Ready to Try It?
Start by tracking just 3 tasks on your next project… and see the impact.
👉 Click here to test PROTRACKBTP for free